Leading through Industry 4.0: How Technology is Changing the Manufacturing Industry
The manufacturing industry is in its most technologically advanced era yet and going through a rapid phase of digital transformation. How we create and produce goods has changed drastically in the last decade, but what technology has made smart manufacturing possible, and how can companies keep up?
The following article provides a deep dive into Industry 4.0 in collaboration with our Executive Guest Contributor, Scott Hicar, Senior Vice President & Chief Information Officer of Benchmark Electronics, Inc. We’ll unpack how Industry 4.0 came to be and explore ways organizations can benefit from adopting some of its principles through leadership and technology.
What is Industry 4.0, the Fourth Industrial Revolution?
Otherwise called the Fourth Industrial Revolution, Industry 4.0 is often referred to as such not just for ease but because it alludes to how we usually name new tech iterations. This latest industrial revolution has been driven and characterized by modern and emerging technologies, including AI, robotics, and the Internet of Things (IoT), as well as by the tailored application of other supportive and innovative technologies, such as automation, big data, and computing.
.webp)
What makes Industry 4.0 so exciting is that it integrates digital, physical, and biological systems into the smart manufacturing process. Biological systems, representing a relatively new and emerging component of the Industry 4.0 revolution, refer to the employment and integration of natural and organic materials, structures, and processes in the manufacturing process. Whether replicating systems and processes based on biological models from nature or leveraging organic material to improve material sustainability, effectiveness, and utility, biological systems are playing an increasingly important role in the evolving manufacturing processes. As a result of the integration of these three systems, this highly automated and data-driven industrial sector can perform real-time monitoring, improve product and process effectiveness and sustainability, and control production processes. This allows companies to maximize efficiency, productivity, and customization while gaining a wealth of data that can be used to optimize these processes further.
That’s why Industry 4.0 isn’t just the result of innovation; it’s also an innovation-reinforcing and feedback mechanism, driving growth for the countries and companies that apply it. It helps them leverage technologies to improve their output and stay ahead of the competition. In a world that moves quickly, Industry 4.0 isn’t just keeping up - it’s continually innovating and improving to push even further ahead.
Looking Back: The Industrial Revolutions 1-3
To better appreciate just how revolutionary Industry 4.0 is, let’s look at what came before it and how industrial revolutions have transformed the market:
First Industrial Revolution
The first industrial revolution, primarily driven by the technological and societal advancements in Europe and the United States, took place during the mid-18th and early 19thcentury and was primarily characterized by the use of coal, water, and steam power. As a result, animal and human labor were replaced for the first time by machinery at a large scale, which ultimately sent many who had once worked on farmlands to operate machinery in factories instead.
Second Industrial Revolution
Often referred to as the Technology Revolution, the second industrial revolution occurred from the late 19th to the early 20th century. The widespread use of electricity and rapid advancements in materials such as steel and other metals and chemicals drove things like the creation of cars, faster trains, and the expansion of major cities. This era was when we first the manufacturing industry take off with production lines that could produce goods faster than ever.
Third Industrial Revolution
The third industrial revolution was spurred by the use of information technologies and, primarily, computing. Mainframe computers began appearing more widely in the 1960s, and with that, a new age was ushered in for data capture and analysis. As computers progressed, we began to see the first iterations of digitized factories using programmable logic in their machinery and other processes.
Although each revolution was viewed as cutting edge at their respective times, it’s amazing to think just how far technologies have come since then with Industry 4.0.
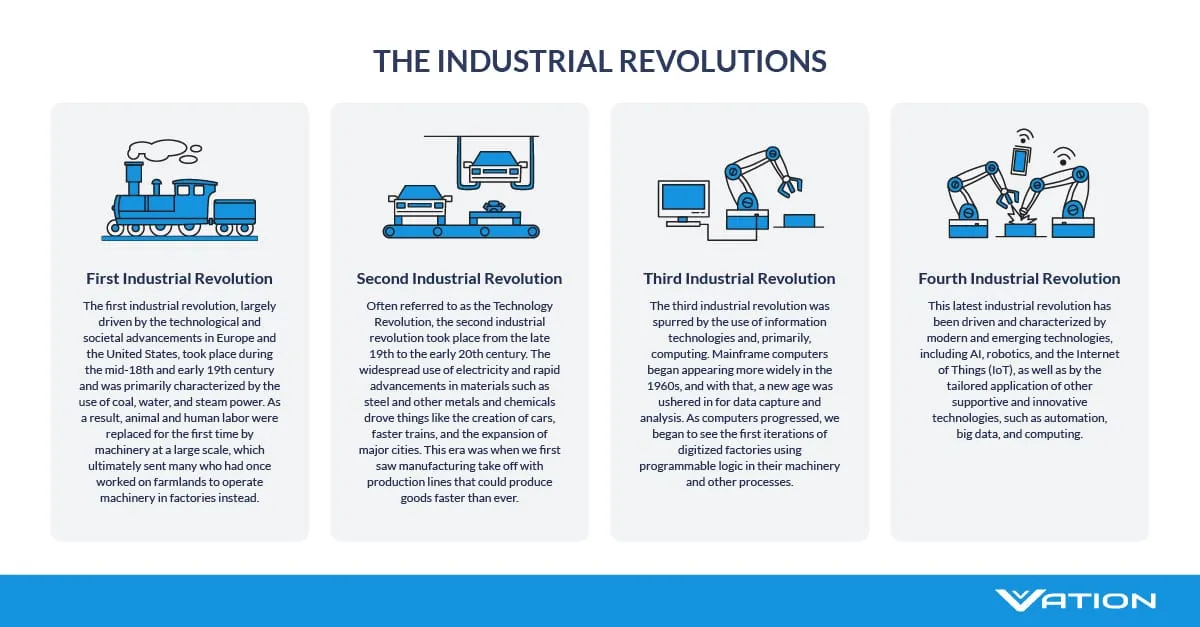
What technologies are driving Industry 4.0?
As we’ve said, Industry 4.0 isn’t defined by one innovation but by the integration of many. Here are some of the key digital technologies driving the Fourth Industrial Revolution:
Internet of Things (IoT)
The clue about this technology is all in the name. Internet of Things (IoT) is about connecting as many things as possible to the internet. When machines each have their own IP address, it allows them to connect with other web-enabled devices, thus creating a myriad of opportunities in data collection, analysis, and optimization. It also encapsulates a key focus of Industry 4.0: connecting the machine and digital worlds to improve overall efficiency.
Cloud Computing
Rather than storing all of the crucial data being gathered and used to inform manufacturing processes on local servers, cloud computing allows everything to be stored online. This saves companies from investing in storage hardware and maintenance while keeping their data safer and more accessible. As long as there’s reliable internet, everything from sales and production figures can be accessed from one place through cloud computing. This makes it far easier to manage large amounts of data and integrate analyses across different areas.
Artificial Intelligence and Machine Learning
The most significant impact that Artificial Intelligence and Machine Learning have had in manufacturing is creating software and machines that can learn from the data they collect. This means that for Industry 4.0, improvement is a constantly ongoing process. Algorithms and the like mean that information gathered can be used to predict obstacles and risks, making operations far less likely to break down without warning. Smart and autonomous systems like this make automation and data exchange smoother and manufacturing more intelligent because fewer errors and opportunities are missed.
Edge Computing
Edge computing is an approach that focuses on doing data analysis at the “edge” of things, i.e., where the data is created. It’s real-time big data collection at the source so that no time is wasted sending data from a piece of machinery to the cloud and then back to the factory site for action. It allows for faster response times to safety issues or breakdowns and, in doing so, minimizes security risks and the chance of unnecessary delays occurring in the manufacturing process.
Cybersecurity
With so much of Industry 4.0 technology being about moving things online, cybersecurity has a significant role. It hasn’t always been given the attention it deserves, but recent years have shown that no matter the size of your organization, you're vulnerable to online threats if you’re using the internet. So much of this industrial revolution is about the value of data. With that comes the need to secure both computers (IT) and operational machinery (OT) from things like malware or cyber-attacks. Industry 4.0 and its new technologies can present additional vulnerabilities without proper cybersecurity systems.
Digital Twin
Manufacturing companies can create digital twins of their manufacturing operations by pulling data from IoT sensors and any devices connected to the internet. Production facilities, supply chains, and factory manufacturing processes can all be replicated digitally and used in testing simulations. Data gathered from these can then inform improvements and predict how processes might perform differently with other inputs, configurations, or circumstances.
Semiconductors
As smart technologies are increasingly adopted, the need for more intelligent electronics at the “edge” has grown. The result of this is that the semiconductor industry is experiencing more demand. Adding to this is the potential this industry has shown for countries wanting to grow their GDP, with the most recent example of this in action being the USA’s CHIPS and Science Act. This new act incentivizes semiconductor research and the local manufacturing of CHIPS because of how crucial they’re becoming in Industry 4.0 and general technological advancements.
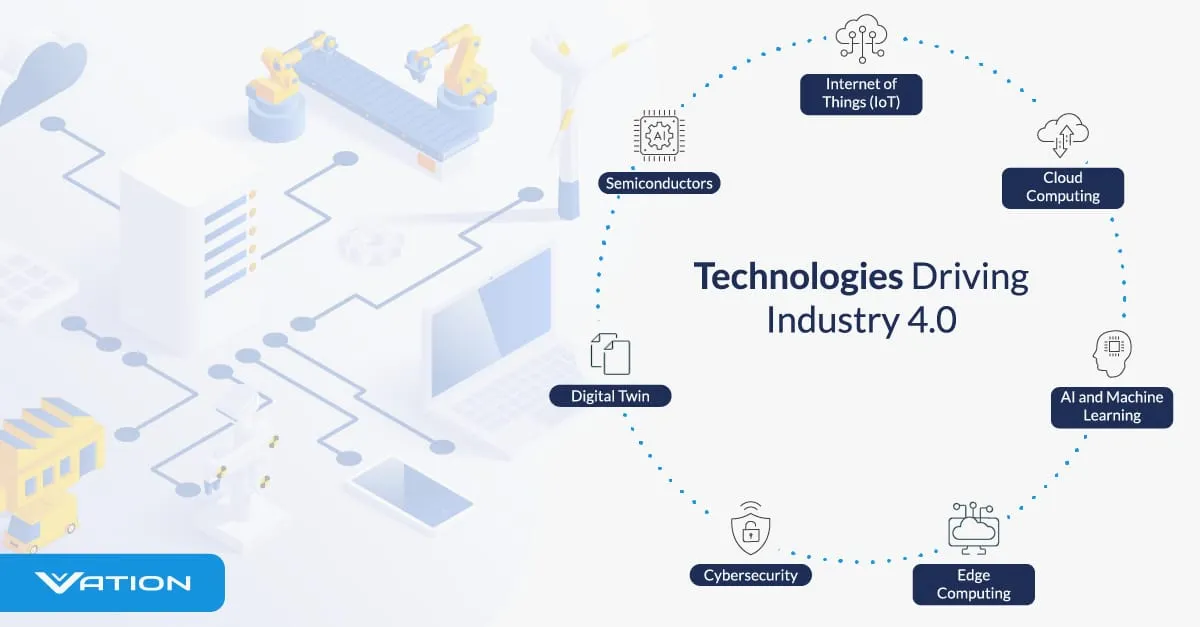
Supply chain issues
One of the most exciting aspects of Industry 4.0 is the change it can offer to one of the biggest manufacturing crises in recent years: global supply chain management issues. The disruptions of the COVID-19 pandemic caused delays across the world, with electronics manufacturers taking the biggest hit as they tried to keep up with the increased demand for chips and electronic components. In addition, the restrictive lockdown and shut-in mandates instituted in China exacerbated and accelerated concerns over Chinese manufacturing dependence, which had already received its fair share of supply scrutiny from the West, given geopolitical concerns. China, in contrast, is investing billions in Mexico to supply the U.S. from closer ports.
.webp)
Mexico is also working with Canada and the U.S. to de-risk supply chains in North America. This makes them far more attractive to manufacturing customers as there’s less chance of significant supply chain issues. This deal and the many problems that inspired it have shown manufacturers the risks of being too lean on supplies and shipping time. It’s also shown how needed Industry 4.0 is for supply chains, given its commitment to real-time monitoring and the use of both digital and machine technology, for anyone trying to stabilize supply chains.
Industry 4.0 and 5G
With all the smart IoT devices being used to collect big data and improve processes in manufacturing, the need for connectivity improvements has grown hugely. That's why 5G has become the new standard for Industry 4.0 in terms of mobile communications and industrial internet. It makes things like uploading data from devices or messages sent between sensors on IoT devices much faster.
As smart technology has improved, so has the volume of data that manufacturers can draw from their machinery and processes. The speed of 5G makes handling all that data far more manageable and, in doing so, increases the usefulness of existing IoT applications. Think about it: what’s the point of real-time data if you’re not getting it quickly enough to use in real time? 5G activation has become a driving force in Industry 4.0 by allowing smart technology to send out information as fast as possible. If we think of the cogs in this new mode of the industry as being smart technology, then 5G is what keeps the system well-oiled.
For many, slow internet prevented smart technology from benefiting their manufacturing processes, but 5G is transforming that. Smart factories, characteristic of Industry 4.0, would not be able to function at the level they do without the improved connectivity 5G offers.
Industry 4.0 Use Case: Smart Factories
“Smart factories” are where Industry 4.0 is at its fullest effect. Sometimes referred to as a “cyber-physical” system, a smart factory makes use of all the innovations that combine both machine and digital operations for a fully streamlined manufacturing approach.
The basic structure of a smart factory relies on three main factors: data acquisition, data analysis, and intelligent factory automation. The technology we’ve discussed, such as IoT, AI, Machine Learning, and 5G, make up the parts of a smart factory and smart machines and allow it to reach a level of productivity, efficiency, and in many cases, sustainably that no other factory model has yet accomplished. They are the ultimate product of Industry 4.0 and all the innovations it’s brought to manufacturing.
How leadership can drive Industry 4.0 within their organization
There are many ways that organizations can implement Industry 4.0 into their digital transformation approach, and much of that starts with leadership:
Create a strategy
To start with, leaders need to clearly understand Industry 4.0 and the potential impact it can bring to their organization. From there, strategies and business processes should be developed that align their business goals with Industry 4.0 principles such as data-driven decision-making, automation, and interconnectedness.
Invest in Industry 4.0
Markets are changing rapidly, and investing time and money in Industry 4.0 technologies is crucial for any leader wanting to advance their organizations. Incorporating artificial intelligence, robotics, and IoT technology can help businesses improve their output and stay competitive in a fast-paced market.
Continuous learning
As technology evolves and advances, leaders need to update their knowledge continuously. The principle of continuous learning also applies to the running of your organization. One of the core aspects of Industry 4.0 is continually gathering data from your operations and using it to fix recurring issues and avoid them in the future. Progress needs to be monitored regularly, and any aspect of the operation that isn’t supporting it needs to be adjusted accordingly.
Organization culture
No amount of new technology can impact a business if the organization's culture isn’t open to it. Innovation needs to be encouraged and woven into a company's business model, and making training and development opportunities available is a great way for people in the organization to stay nimble. In addition, so much of Industry 4.0 relies on the collaboration of different technologies, but putting that into action requires cross-functional teams where collaboration on ideas is also fostered.
Industry 4.0 is about innovation and improvement
Whether we’re talking about 5G, linking digital technologies and machine processes, or the advancements of IoT, the core aspect of Industry 4.0 is continuous innovation and improvement. This doesn’t simply start with technology, though; leadership and organizational culture play a huge role too in developing new Industry 4.0 business models. The true innovation of Industry 4.0 is bringing all these aspects together to change traditional manufacturing from the inside out. Looking to know more about how Industry 4.0 is changing the technology landscape? Learn more about Industry 4.0 and the emerging technologies disrupting the space in our Platform. Book a demo today.